A broken sway bar can cause significant handling issues in your vehicle, making driving unsafe. The answer isn’t simple if you’re wondering whether you can weld a broken sway bar. In this guide, we’ll break down when welding is a good option, how to do it safely, and when it’s better to replace the sway bar entirely.
Is It Possible to Weld a Broken Sway Bar?
Yes, you can weld a broken sway bar, but it depends on the material and severity of the break. Welding should only be done by someone experienced, as improper repairs can weaken the sway bar and compromise safety.
Table Of Content
- What Does a Sway Bar Do?
- Can you fix a sway bar yourself?
- Best Welding Methods for a Sway Bar
- How to Successfully Weld a Sway Bar
- Alternatives to Welding a Broken Sway Bar
- Signs You Should Replace Rather Than Weld
- Preventing Sway Bar Damage in the Future
- DIY vs. Professional Repairs: When to Seek Help
- Cost Analysis: Welding vs. Replacement of a Sway Bar
- FAQs: Your Questions Answered
- Conclusion
What Does a Sway Bar Do?

A sway bar, also known as an anti-roll bar, reduces vehicle body roll during turns, improving handling and stability. It connects the left and right wheels, keeping them balanced as you drive.
Sway bars are essential for preventing excessive body roll during sharp turns.
They help maintain vehicle stability, especially in cornering and when driving on uneven roads.
A broken sway bar makes the vehicle harder to control, increasing the risk of accidents.
Can you fix a sway bar yourself?
Yes, you can fix a sway bar yourself, but it depends on your experience and tools. Minor issues like replacing bushings or end links are DIY-friendly.
if the sway bar is cracked or broken, you should have proper knowledge of welding, cutting and grinding tools.
Best Welding Methods for a Sway Bar
The best welding method for a sway bar is TIG welding, which is known for its precision and strength. For sway bars made of high-carbon steel, MIG welding can also be effective.
TIG (Tungsten Inert Gas) welding is often the top choice due to its precision and ability to produce high-quality welds on delicate components like sway bars.
This method uses a tungsten electrode and provides superior heat control, making it perfect for welding steel or other metal sway bars.
For sway bars made of high-carbon steel, MIG (Metal Inert Gas) welding can also be a good option. MIG welding is typically faster and easier to learn than TIG, but it requires less finesse. It’s effective for sway bars because it can produce strong welds quickly, though the quality might not match TIG in terms of neatness and control.
How to Successfully Weld a Sway Bar
Preparation: Clean the broken area, removing any dirt, grease, or rust. Drain any fluids near the welding zone.
Choose the Welding Method:
- TIG welding is ideal for thin metals and offers precision, making it great for sway bars.
- MIG welding, on the other hand, is faster and easier to execute for those with less experience. Consider the sway bar material- steel, aluminium, or high-carbon steel, when deciding which method to use.
Align the Break: Ensure both ends of the broken sway bar are properly aligned before welding to prevent imbalance.
Welding Process: During the welding process, maintain a steady hand and apply controlled heat along the crack. Start from one end and move steadily to the other, allowing the metal to melt and fuse. It’s essential to avoid overheating, as this can weaken the surrounding metal. If using TIG welding, ensure your tungsten electrode is sharp and your settings are appropriate for the material thickness.
Post-Weld Inspection: Check the weld for any weak spots or imperfections and test the sway bar’s strength before reinstalling.
Alternatives to Welding a Broken Sway Bar

If welding a broken sway bar isn’t an option, replacing the sway bar entirely is a safer and more effective solution than welding.
A replacement ensures that the sway bar functions as intended, maintaining your vehicle’s handling and stability.
Always assess the damage before deciding on a solution.
Signs You Should Replace Rather Than Weld
Replace the sway bar if it shows signs of extensive corrosion, or if multiple breaks are present. Welding may not hold in these cases, and replacement is a safer option.
Rust and corrosion weaken the sway bar’s structural integrity, making it more prone to breakage.
If the sway bar has been repaired before or is significantly worn, welding might not provide a reliable fix.
Check for additional suspension issues- if the sway bar is damaged, other parts of the suspension might also require repairs.
Preventing Sway Bar Damage in the Future
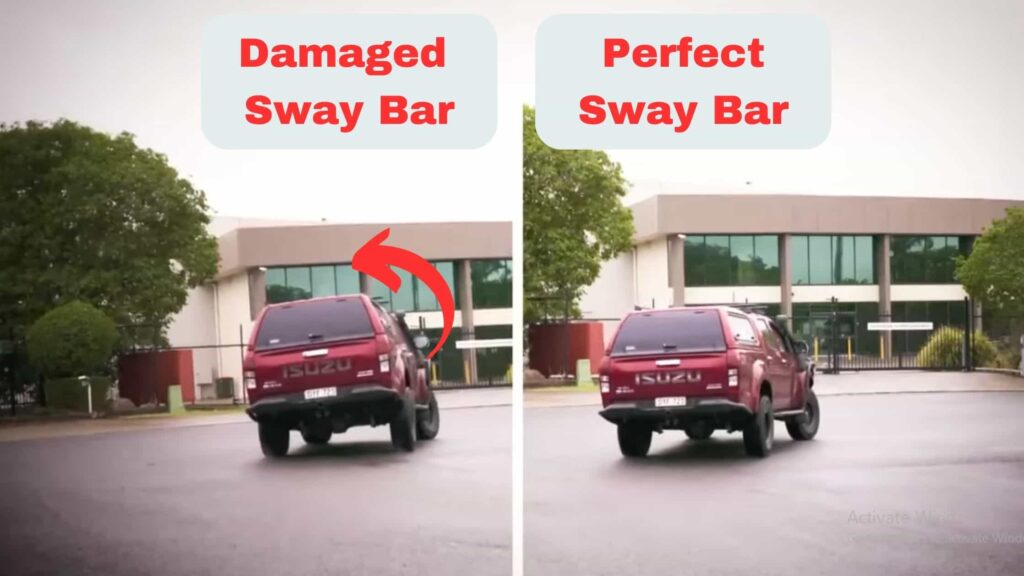
Regular vehicle maintenance, such as checking sway bar bushings and avoiding overloading your vehicle, can help prevent future sway bar damage.
Inspect sway bar bushings regularly to catch early signs of wear. Avoid overloading your vehicle or taking sharp turns too fast, as these put stress on the sway bar.
Upgrading suspension components can also improve sway bar longevity, reducing the risk of future damage.
DIY vs. Professional Repairs: When to Seek Help
Deciding between a DIY repair and hiring a professional can be challenging, especially when it comes to critical vehicle components like the sway bar.
Here’s a closer look at the considerations to keep in mind:
1. Skill Level and Experience
DIY Repairs: If you have a solid understanding of automotive repairs and the necessary tools, you might feel confident to repair it by yourself. DIY repairs will save money and provide a sense of accomplishment.
Professional Repairs: If you lack experience or are unsure about the repair process, it’s best to consult a professional. They have the training, knowledge, and expertise to assess and fix complex issues.
2. Severity of the Damage
Minor Issues: For minor repairs, such as small bends or non-critical cracks, a DIY approach is sufficient. If the damage is minimal and you feel capable of making the fix, go for it!
Significant Damage: If the sway bar is severely damaged, professional assistance is advisable. A professional can accurately assess the structural integrity and recommend the best course of action, whether that’s repairing or replacing the sway bar.
3. Safety Considerations
Safety Risks: A sway bar plays a crucial role in vehicle stability. If the repair isn’t done correctly, it can lead to serious safety issues while driving. If you have any doubts about your ability to repair it safely, you should seek professional help.
Long-Term Implications: A poorly executed DIY repair may save you money upfront but can lead to more costly issues in the long run. Professionals will ensure the repair meets safety standards, providing peace of mind.
4. Cost vs. Value
Cost of Tools: Consider whether you have the necessary tools for the job. If you need to purchase specialized equipment, it might make more sense financially to hire a professional.
Value of Professional Work: While professional repairs may seem more costly initially, they often come with warranties and guarantees. This can save you money on future repairs and provide added assurance that the job is done correctly.
5. Time Commitment
DIY Repairs: Depending on your skill level, a DIY repair can take a significant amount of time, especially if you are repairing it first time. If you’re not pressed for time and enjoy the process, this might be a viable option.
Professional Repairs: Hiring a professional can save time and hassle. They can often complete repairs quickly and efficiently, allowing you to get back on the road sooner.
When weighing DIY versus professional repairs for your sway bar, assess your skill level, the severity of the damage, safety considerations, cost, and time commitment. Sometimes, enlisting a professional is the best way to ensure a safe and reliable fix for your vehicle.
Cost Analysis: Welding vs. Replacement of a Sway Bar
When dealing with a broken sway bar, it’s important to weigh the costs of welding versus replacement. Here’s a quick breakdown:
Welding Costs
Labour: If you’re hiring a professional to weld the sway bar, labour costs will vary depending on the mechanic and location. Expect to pay anywhere from $20 to $80 for the welding work.
If you decide to DIY, you’ll need to factor in the cost of welding tools (TIG or MIG), welding rods, and other materials, if you don’t already own the equipment.
Risks: Poor welding can lead to future failures, requiring more repairs.
Replacement Costs
New Sway Bar: A new sway bar costs between $100 and $300, depending on the vehicle. Labor for installation adds another $50 to $150.
Long-Term Value: Replacing the sway bar ensures better durability and safety, making it a more reliable option.
FAQs: Your Questions Answered
1) Can I drive with a broken sway bar?
It’s not recommended to drive with a broken sway bar. While the vehicle will still move, its handling, especially during turns, will be compromised, increasing the risk of accidents.
2)How do I know if my sway bar is broken?
Signs of a broken sway bar include clunking noises during turns, poor handling, and excessive body roll when driving.
3) How long does a sway bar last?
A sway bar typically lasts the lifespan of the vehicle, but wear and tear on sway bar links and bushings may require replacement after 50,000 to 100,000 miles.
4) Can I replace a sway bar myself?
Yes, if you have the right tools and experience, you can replace a sway bar yourself.
5) Can you bend a sway bar back into place?
Bending a sway bar back into place is generally not recommended. Sway bars are designed to be rigid, and bending them can weaken the material, compromising their effectiveness and safety. If a sway bar is bent, it’s usually safer to replace it rather than attempt to reshape it, as it may fail under stress.
Conclusion
Yes, welding a broken sway bar can be a good option, if done properly. A well-executed weld can restore the sway bar’s strength and help extend its lifespan. However, it’s important to understand the risks involved, as an improper weld could lead to failure. On the other hand, replacing the sway bar is often a safer, more reliable solution, especially for long-term durability. Ultimately, the choice depends on the condition of the sway bar and your comfort with the trade-offs between cost and safety.